Customer: NOAA/NMFS
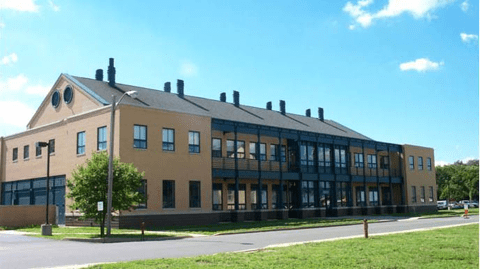
Burgos Group provides all trade employees with the necessary skills and training to assist NMFS in the operation, maintenance, repair and upkeep of James J. Howard lab’s buildings and equipment as required. These certifications include, but are not limited to lockout/tagout, asbestos and lead awareness, confined space awareness and hazard communication; and other training as required by OSHA. Support includes but not limited to: Maintenance, repair, and services for office building, laboratory building, seawater intake system (including pumps, piping, pump pit and seawater intake wells heads), compressors, infrastructure systems (generators, cooling towers, electrical systems, switch gear, plumbing, piping, HVAC, boilers, day tanks, underground fuel storage tanks and fuel delivery systems, seawater tanks, filtration systems, lighting systems (some computer controlled), controlled temperature rooms, distilled water system, compressed gas systems, freezers, fume hoods and other components required to keep operations going.
The laboratory consists of two (2) buildings, Building 74 and the JJH Laboratory building. The James J. Howard Laboratory is a state-of-the-art marine research facility shared by NOAA and the State of New Jersey.
This was a new federal contract requirement as the services had previously been performed under a state contract; however, due to end of year funding crunch pressures our contract mobilization schedule was compressed to 14 days to meet the customer’s needs to be up and running on Day One of the performance period. During this 14 day period, we were able to execute two collective bargaining agreements and ensure all personnel, materials, supplies and equipment – including vehicles – required for contract performance were onsite.
We have saved the customer money by minimizing cost-reimbursable purchases requirements through the design, implementation and maintenance of inventory controls, which did not previously exist. Also, we implemented a work order system to streamline the approval process of required maintenance repairs resulting in reduced facility down time.
More than a dozen emergency maintenance requirements have arose since the contract award (September 2016). We have resolved each and every one of these in accordance with the contract performance standards, which require 24/7 availability and an onsite response within two hours.